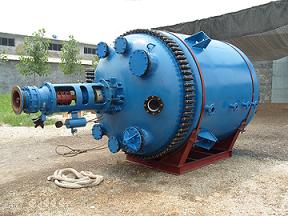
搪玻璃反应罐是国家一、二类压力容器,有其本身的特性,并通常进行腐蚀性很强或易燃易爆物料的使用,在搪玻璃反应罐操作使用前必须对操作工人进行上岗前的培训,才能保证对搪玻璃反应罐的正确使用,并能进行正确的日常维护和定期清洁,使各项具体操作标准化和规范化,才能延长搪玻璃反应罐的使用寿命,有利于安全生产的保障以及稳定产品的质量,作为国内专业的搪玻璃化工设备生产厂家,为保证广大用户的生产安全和经济效益,我公司结合搪玻璃反应罐的特性特制定出以下搪玻璃反应罐操作的岗前培训内容,以供广大客户参考。一、要了解什么是搪玻璃,什么是搪玻璃反应罐,搪玻璃反应罐的结构和特性。简而言之,搪玻璃反应罐是将含二氧化硅高的瓷釉喷涂在钢制胚体上经特殊工艺烧制而成一种优良的耐腐蚀反应容器,其构成分体盖或体盖一体,配有夹套以加温或冷却,配有搅拌传动系以混合物料加速物料反应,搅拌系统包括电机、减速机、密封、搅拌,配有温套管内置热电偶随时检测罐内物料的温度,罐盖上有各种用途管口,底部配有放料阀;搪玻璃反应罐属国家一、类压力容器,要熟知其承压和耐温范围,其适用范围等等,这些要通过认真学习厂家提供的说明书和操作规程熟练掌握。二、使用前的准备工作: 首先,要对设备进行检查:检查并确认设备及附件的外观无异常,各连接处卡子数量足够并连接紧固,螺栓连接处无明显松动,视镜要干净,各接口处依据要求密封完好、无泄漏,搅拌桨锁紧螺母无松动。 其次,要对电机及其开关等电器进行检查:检查并确认搅拌电机外观完整、接地线接好、电源线完整、搅拌器开关完好、釜盖与釜体间及减速机、搅拌电机间的静电接线完好,试验并确认视孔灯完好。使用易燃易爆物料时,应确认搅拌电机为防爆电机,并已按防爆要求进行接线和配置防爆开关,否则严禁使用。 第三,要检查传动系统的润滑情况:检查填料密封处填料压盖是否已到底,单端面机密封的油杯内是否有油,双端面机械密封的润滑系统中油量是否充足以及冷却水是否正常循环,减速机内油量是否到达油视窗三分之一处,各润滑系统有无漏油处。 第四,要检查管线配置的情况:检查各联接管线上的阀门、管线、管件和保温层是否完好、有无泄漏处,手动阀门的操作手柄或手轮是否完好,阀门是否处于关闭状态、阀门的开启和闭合是否顺利,安全阀是否处于关闭状态,所需用的公用工程是否已准备好。 第五,要检查各个仪表,检查并确认温度、液位、压力及其他仪表的显示处于正常状态,相关指示正确。 第六,是对初次试车的要求,应先用手盘动电机,带动搅拌器转至少一圈以上,观察并确认搅拌器转动时无异常声响,且不与罐内任何物件相碰。初次试车时要以水代料加入罐内进行运转检查传动系统是否正常,各连接处密封是否良好。三、 正式投料生产: 首先要试启动:点动搅拌器开关,检查并确认搅拌器运转方向正确(如采用外循环强制润滑系统进行减速机或密封的润滑,应在启动搅拌器前启动外循环装置),严禁搅拌与减速机铭牌上的旋转方向相反,如果倒转则换接电机接线,否则搅拌有脱落损坏整个罐体的危险。 试启动完毕,严格按工艺要求将物料投入罐内(一般罐内物料不宜超过全釜容积的2/3,对于开式搪玻璃反应罐,物料在搅拌状态下的液面不宜高于反应釜体与釜盖的法兰面),启动搅拌电机,按工艺要求通入加热或冷却介质,控制温度、压力和反应时间,同时进行其他相关操作。对于10000L以上的大罐,或搅拌有底轴承的要等物料液面才能启动搅拌电机,严禁空转。 反应完毕后,严格按工艺要求向夹套内进冷却水或冷冻冰盐水,将物料的温度降到工艺要求后,打开放料阀,放出或移走物料。三、 操作中的注意事项: 首先,搪玻璃反应罐在使用过程中严禁温度骤冷、骤热,以免损坏搪玻璃面。搪玻璃反应罐耐温急变(即反应罐温度与加热或冷却介质温度之间差)为:冷冲击≤110℃,热冲击≤120℃。在通入蒸汽加热时,夹套内的水要先放净。开启蒸汽或冷却水进口阀时,不可一次性全开,要预先通入至夹套压力在0.1MPa左右,保持数分钟后,再分次缓慢开启进口阀,以防止冷热冲击损坏设备。升温(或降温)速度应保持在3℃/分钟左右,最大不宜超过5℃/分钟; 第二,反应过程中要随时巡回检查严禁离人,要严格执行生产工艺操作规程,要密切注意罐内和夹套内的工作压力和温度,严禁超温超压;若发生超压,则赶紧打开放气阀泄压至规定范围内,若发生超温则赶紧减少加热量或暂停加热,或用水降温等使温度降至工艺允许范围内; 第三,严禁敲击搪玻璃面或其外壳,操作时应防止螺栓、扳手等硬物掉入釜内损坏搪玻璃面; 第四,生产中若突然停电,要停止投放后续物料,若投料途中停电,停止投放一切物料,打开放气阀给水降温; 第五,操作中尽量避免釜体外壳与酸、碱等腐蚀性液体接触,一旦有物料接触应及时用抹布擦洗干净; 第六,对于有保温层的反应罐禁止用水冲洗设备,避免保温层损坏; 第七,在开启人孔或手孔时,人孔或手孔盖的搪玻璃面应面向下放在由软木做成的支架上或软垫上,不可使搪玻璃面直接放在硬地面或钢平台上,或是将搪玻璃面向上放置。拆下的卡子应就近整齐放好,不可妨碍操作或行走; 第八,操作过程中应经常观察温度计套管是否与物料接触。由于搪玻璃管的热阻较大,一般罐内的温度显示与实际温度有一定程度的滞后,升温、降温操作时应考虑到热惯性和显示滞后因素的影响; 第九,冬天操作时当最低气温≤0℃时,应在使用完毕后放尽夹套内的存水,避免设备因冰冻而损坏; 第十,对于装配有机械密封(单机封或双机封)的反应罐,密封部位应保持清洁; 第十一,出料时如遇罐底堵塞,不应用金属器具打,可用竹竿或塑料棒、木棒轻轻捅开。出料时如发现有搪玻璃碎屑,应立即开罐检查,修补后再用; 第十二,检修时,要在罐底铺设软垫,以免工具掉落损坏搪玻璃面,并严禁穿戴钉子或沾有沙粒的鞋子进入; 第十三,搪玻璃反应罐及其它搪玻璃设备不适用于下列介质或物料的反应、聚合、贮存、换热等化工过程: (1)任何浓度和温度的氢氟酸及含有氟离子物料; (2)浓度大于30%、温度大于180℃的磷酸; (3)PH值大于12且温度高于80℃的强碱; (4)酸碱物料交替进行的反应过程,如果一起进行则中和没有问题。 第十四,要严格做好交接班记录,交接双方在交接时一定要共同查看反应罐的使用情况以及确定好后续的工作,双方都要签字并标明具体的交接时间。四、 日常的维护操作: (1)以每天运行16小时计,新反应罐运行一周后减速机油杯内的润滑机油要全部换掉,以后每隔3个月或根据具体使用情况重换,40号-50号机油均可; (2)检查接管、法兰、阀门,更换泄漏处的垫圈、阀门、填料,并紧固松动的螺栓; (3)检查传动系统各部件有无松动,搅拌器手动盘车是否轻松,搅拌桨摆动量是否过大; (4) 检查在运行中有无异常声响; (5) 检查润滑部位并按时依照标准加注合格的润滑油,润滑油量应保持在油视窗1/3处; (6) 检查填料和密封状况,检查外露的机械密封弹簧是否受腐蚀,调整机械密封动环压紧量; (7)检查各仪表工作是否正常并定期校验; (8) 检查夹套有无泄漏、穿孔,修补保温层并补好油漆; (9)查搪玻璃表面有无明显破损,设备的外表面有无腐蚀处; (10)定期检查电机接线是否完好,电机、电线绝缘是否完好,接地电阻值是否符合规定。 (11) 若长时间停车不使用,要将罐内残留物料放净,并清洗干净,关闭进气阀,进料阀,放料阀 注意:严禁在反应过程中带压紧固各部受压元件。五、 常见故障的表现、原因及处理: 第一, 超温、超压: (1)违反工艺要求,严重超时加热或反应:要严格执行生产工艺要求,在限定的范围内操作; (2)违反工艺要求原料配比不当,造成剧烈反应:立即停止加热操作,注意保持反应釜放空阀通畅,必要时通过降温减缓或终止反应,按工艺要求处理物料。 (3)仪表失灵,控制不严格: 检查、修复控制系统,严格执行仪表校验管理规定; 第二: 密封不严、漏水、漏气、漏料: (1)填料磨损或质量差:更换填料; (2)阀门、法兰等密封面不严:更换阀门、法兰、垫片; (3)机械密封泄漏或密封液向罐内泄漏:检查机械密封的密封面和静密封件,调整动环压紧量; (4)设备本体发生腐蚀:修理或更换; (5)设备联接附件或管件阀门泄漏:检查并处理; (6)罐卡子松动或数量不足,接口螺栓松动或数量不足:紧固或补足卡子或螺栓. 第三,罐内发生异常声响: (1) 搅拌器摩擦罐内附件、搅拌轴弯曲变形、搅拌器松动:停车检查、校正、修理并紧固螺栓; (2)轴承损坏:修理或更换轴承; (3)釜内有异物:停车,清理釜内异物; 第四,罐体或衬里鼓包: 停止使用,由专业维修人员处理. 第五,声音大或振动: (1)螺栓松动: 紧固联轴节螺栓; (2)间隙过大: 调整联轴节间隙或更换联轴节.六、清洁工作: (1)当班人员在设备正常运行时若发现机封、减速机等部位出现污痕要随手及时清除,车间主任或班组长要随时检查; (2) 每批生产结束后,对有保温层的反应罐要用抺布将设备外壁擦洗干净,禁止用大量的水连续冲洗设备外部,避免保温层损坏。 (3) 按工艺要求,生产一定时间后,应对反应釜内进行清洗。较长时间(≥72小时)停产后,开班前设备应重新清洗。 (4) 清洁标准:单个品种使用(专用)的设备清洗至不能发现可视杂物;多个品种使用(公用)的同一台设备在更换品种时按工艺要求执行。 (5) 清洗操作人应及时填写清洗记录,经验收人(当班班长、接班人员或设备管理人员)验收并签字确认。 当然,每个客户都有自己的生产工艺和设备配套,对搪玻璃反应罐有着自己的使用要求,我们可以一起探讨完善,制作出适合您的安全操作条例以便您进行有效的岗前培训,这样对提高您的安全生产、延长设备的使用寿命、创造出更大的经济效益将提供强有力的保障。恭祝广大客户万事如意大发展,社会效益经济效益双丰收。 淄博森宇化工设备有限公司 技术部